Cold Cutting
Cold Cutting
Cold cutting is an advanced, environmentally friendly technique for cutting steel, composites, and concrete using Ultra High-Pressure Water Jetting combined with abrasive materials. This process generates no heat, making it ideal for environments containing chemical vapours, degassing substances, or other volatile elements. Aqua Prep offers a cold-cutting service that provides a cost-effective and safer alternative to traditional hot-cutting methods, particularly in situations involving chemicals and explosive vapours.
Aqua Prep’s cold-cutting technique allows for faster re-welding of surfaces and produces less hazardous waste. It stands out as the most dependable option in the industry because it preserves the metallurgy of cut materials. With extensive experience in diverse environments, from sewers to petrochemical plants, Aqua Prep utilises state-of-the-art water jetting machines and cold-cutting equipment to achieve superior results. Their equipment can cut high-tensile-strength steel and thick concrete blocks with precision, and they have also completed underwater projects for ships and offshore rigs.
The critical benefits of cold cutting include rapid and safe execution, elimination of grinding requirements, prevention of heat-affected zones, and an environmentally friendly methodology. Aqua Prep’s remote-controlled water jetting Cold Cut system delivers unparalleled ultra-high pressure (UHP) water jetting for any cold cutting project. To enhance precision and safety, they incorporate a water-abrasive mixture into the cold-cut head.
Cold cutting is often preferred in explosive environments for several reasons. It prevents sparks, generates minimal heat, produces larger chips rather than fine dust, can be pneumatically or hydraulically powered, uses non-flammable lubricants or coolants, allows for greater control and precision, and is often ATEX (Atmospheres Explosible) compliant.
In contrast, wire and concrete cutting methods can produce sparks, generate heat through friction, create fine airborne dust, require electrical power, need water for cooling, and have a more aggressive nature that could potentially damage surrounding structures. These factors make them less suitable for use in explosive atmospheres.
Given these factors, cold cutting is often the safest choice in explosive environments. It minimises the risk of ignition sources while still allowing necessary cutting operations. However, it’s crucial to note that even with cold cutting, all equipment must be appropriately rated for use in the specific hazardous area classification of the work environment.
Cold Cutting
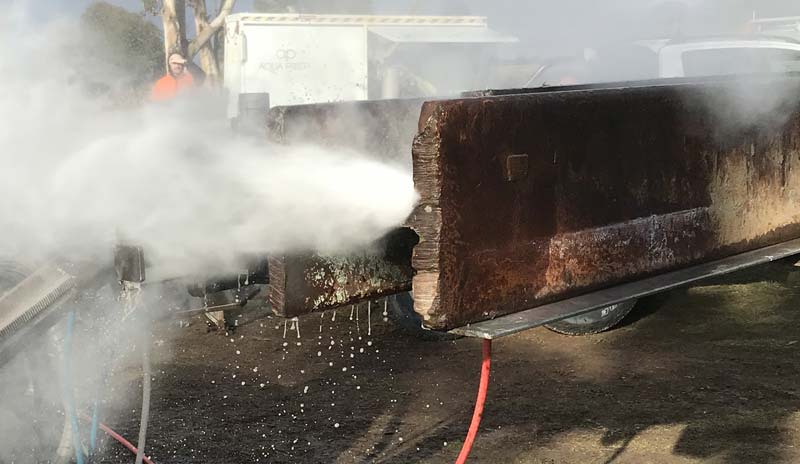
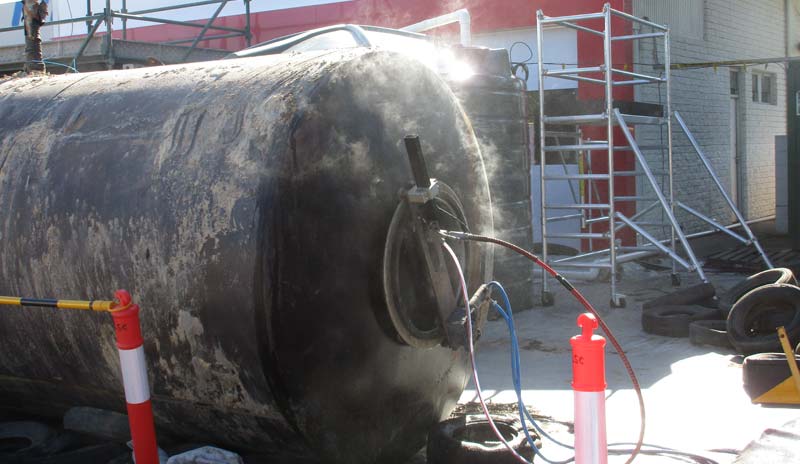
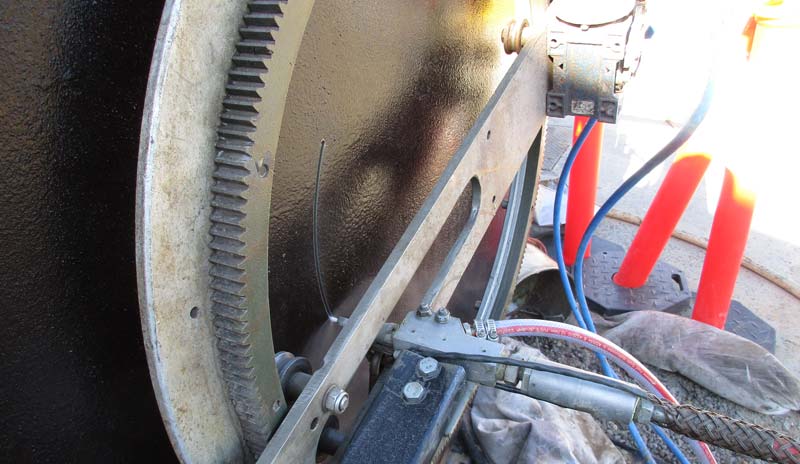
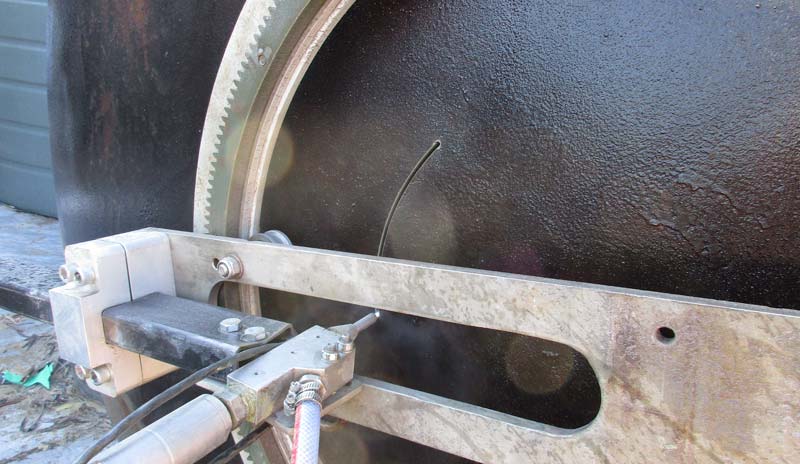
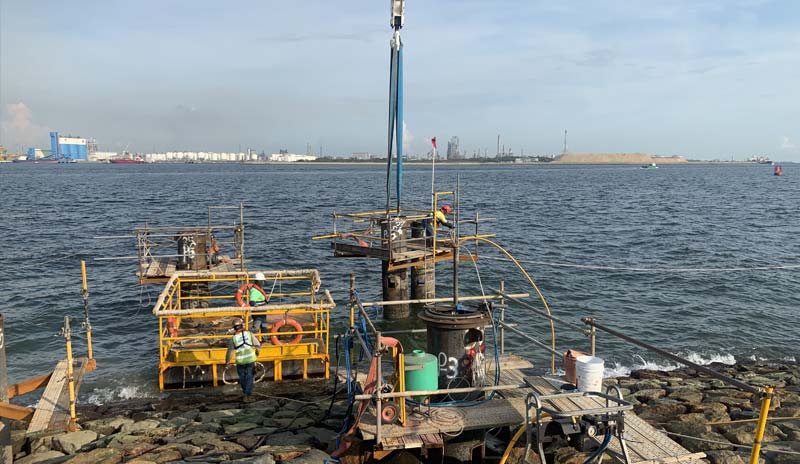
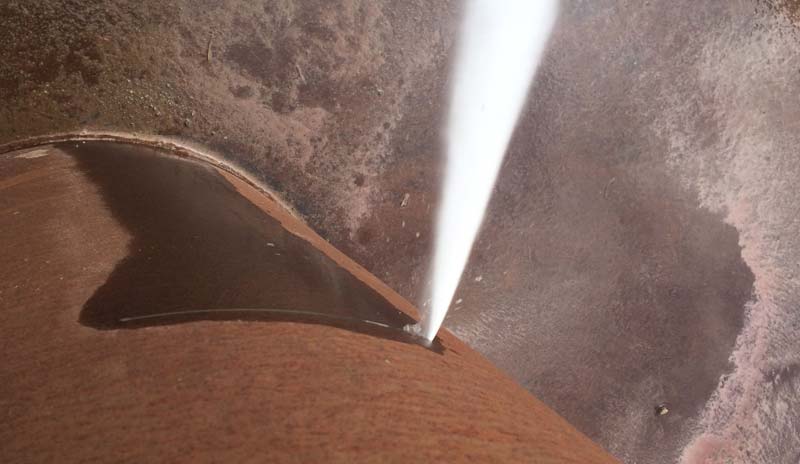
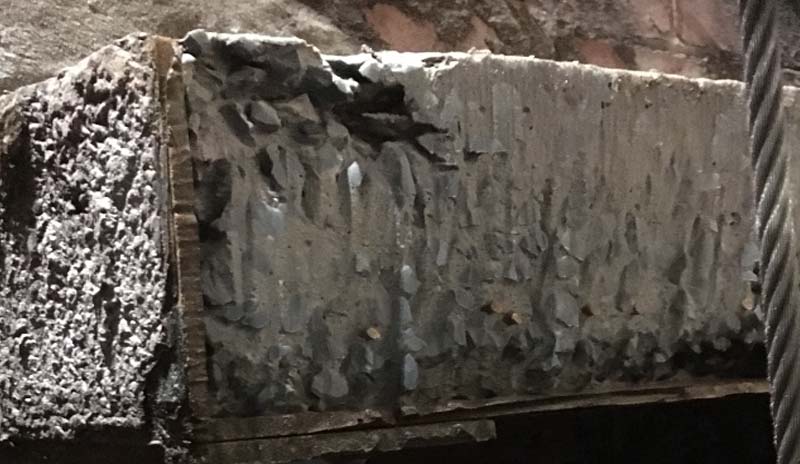
7.5+
Revenue in 2023 (Million)
50+
Collaegues & Counting
1200+
Successfully Projects
200+
Years of combined experience
FAQs
Cold cutting is a precision cutting technique that doesn’t use heat, flame, or sparks, making it ideal for sensitive environments. Unlike traditional cutting methods that involve grinding or oxy-acetylene cutting, cold cutting services eliminate the risk of thermal damage, ignition, or warping, which is crucial in industrial or explosive-prone settings.
Our cold cutting services, available nationwide, can be applied to a wide range of materials, including concrete, steel, metal pipes, tanks, and composite surfaces. This method is particularly suitable for projects that require minimal vibration and noise, such as those in hospitals, live industrial plants, or fuel storage sites.
Aqua Prep is trusted across Australia for delivering safe, precise, and efficient cold cutting services. We utilise industry-leading technology and experienced operators to ensure clean cuts with zero heat distortion. Our team also adheres to strict safety standards, making us an ideal choice for high-risk and regulated environments.
Yes, cold cutting is specifically designed for hazardous or explosive environments where traditional hot cutting methods pose safety risks. Our cold cutting services are spark-free and flame-free, reducing the risk of ignition when working near flammable materials, gases, or confined spaces.
Absolutely. Cold cutting is commonly used for structural modifications, dismantling, and decommissioning industrial assets like pipelines, tanks, and reinforced concrete. Our cold cutting specialists in Melbourne ensure precision and safety throughout every stage of the cutting process, even in complex or hard-to-reach areas.
Yes, we offer detailed onsite assessments across Melbourne to evaluate your cutting requirements, surface conditions, and safety factors. Our team will determine the most suitable cold cutting method and equipment, ensuring your project is completed safely, efficiently, and on time.